[Ferro-Alloys.com] Carbon is increasingly acquiring a cost that will eventually be built into steel production all over the world.
This is welcome, given the need to reduce carbon emissions — the energy intensity of crude steel needs to fall by 1pc/yr between 2017 and 2030 to be on track with the International Energy Agency's sustainable development scenario.
But it also poses a dilemma. In a global market such as steel, a level playing field is necessary to ensure production does not leak from regions where carbon has a cost, to those where it does not.
Where there is no level playing field, structurally higher steelmaking costs are harder to be passed on.
Implementing mechanisms that give a cost to carbon and incentivise greener production can hurt producers if they are competing against mills with a structurally lower cost base.
"Any carbon costing mechanism is a very difficult system to implement in an equitable and fair way — how [do] you account for carbon costs that are carried in some regions in a different way, how do you deal with them in a fair way," the director-general of industry association Worldsteel, Edwin Basson, told Argus.
He suggested any scheme needs to be flexible enough to allow the trade and flow of steel to continue. "Whatever the system is, I still believe it should pass muster in terms of a World Trade Organisation (WTO) approach, and be applicable under WTO rules," Basson said.
Different mechanisms are being considered to prevent leakage to markets where carbon has not yet acquired a cost, such as the carbon border tax in the EU. Global steelmaker ArcelorMittal has lobbied hard for the introduction of this mechanism, suggesting that the world will continue to rely on current primary sources to produce steel in 2050.
More than one way to cut emissions
There is no single technology to reduce carbon emissions in the steelmaking process, and many different routes will be employed going forward, Basson said.
Several European producers have focused their efforts to reduce emissions on hydrogen-based steelmaking. But ArcelorMittal has adopted a multi-track strategy, as it has never viewed hydrogen as the only route to reducing emissions, or that green hydrogen — produced through renewable sources — will be readily available at competitive prices. The technology utilised will differ depending on the region and respective access to different fuels and technologies, Worldsteel said.
In the short term, ArcelorMittal is focusing on increasing the scrap charge in its furnaces, and the use of smart carbon technology, such as carbon capture, utilisation and storage. Longer-term, to achieve carbon neutrality by 2050, the firm will try to harness hydrogen-based production alongside smart carbon. ArcelorMittal recently said it will supply 30,000t of "green steel" this year, with the emissions savings primarily attributable to hydrogen injection.
ArcelorMittal suggests its smart carbon approach will increase costs by 30-60pc, while using the innovative hydrogen-fed direct reduced iron route will see costs rise by 50-80pc.
Emissions reductions and the consequent transition to higher costs will have ramifications for the steel product mix, Basson said. But mills cannot just stop making "bread and butter grades" that have existed for decades and are used in a variety of applications, he said.
Source: Argusmedia
********************
The 2nd China Manganese Rich-Slag Technology Innovation and Policy Summit
Beijing, China Oct. 30-31 2020
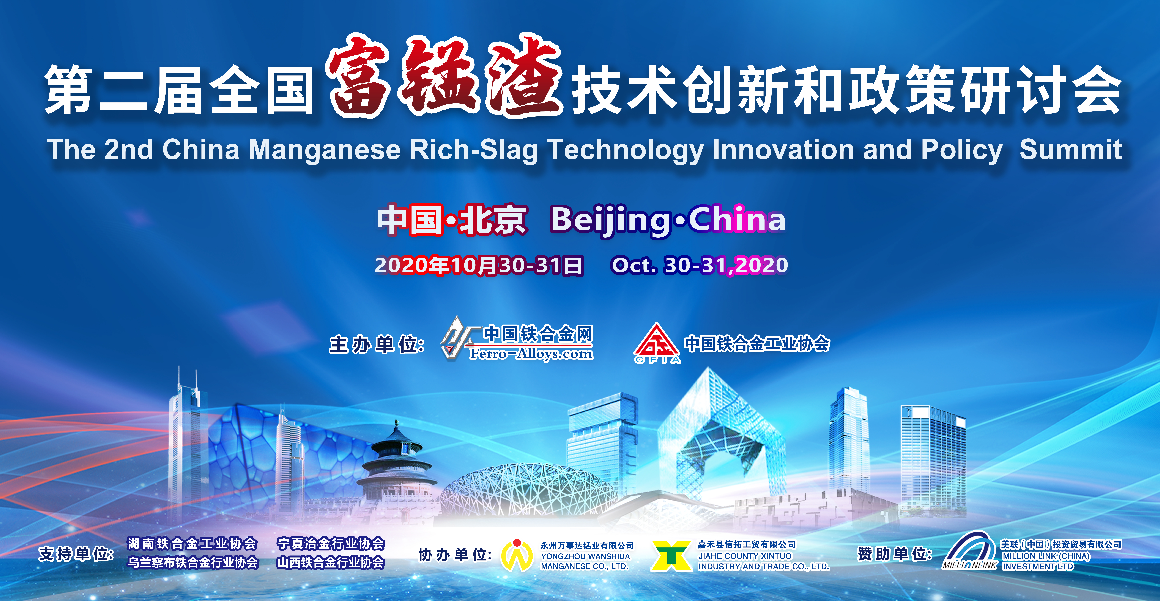
Copyright © 2013 Ferro-Alloys.Com. All Rights Reserved. Without permission, any unit and individual shall not copy or reprint!
- [Editor:kangmingfei]
Tell Us What You Think