中国铁合金网讯:
从某种意义上说,自动化、信息化和智能化有着共同的理论基础,但面临问题的尺度却不一样。从尺度的角度,有助于我们认识智能化的发展方向和技术特点。
1 理解自动化
20世纪40年代,控制论之父、美国数学家维纳开始考虑普通的机器与人(或动物)有什么不同?他的答案是,传统机器只能按照既定的逻辑运行,而人(或动物)则可以根据外部的变化采取适应性的行动。所以,要让机器代替人的工作,机器需要有感知信息的能力,并能够根据信息进行决策,并采取行动。也就是要把信息的感知、决策和执行过程统一起来。按照现在的说法,就是要把负责信息感知、处理的赛博空间与执行指令的物理空间相结合,这就是控制论的基本思想。
这种思想的产生并非偶然,而是基于弱电技术的支撑。弱电可以用来表达和处理信息,并转化成强电驱动物理空间的机器运转。
从某种意义上说,机器自动执行时的工作逻辑,都是人类预先设定的预案、在人类规定的“边界”内部执行。只有这样,人类才能放心地把工作交给机器自动完成。
2 企业的计算机系统
钢铁企业的自动化与计算机系统早已密不可分了。在钢铁企业中,计算机系统一般被分成若干级别。最常见的做法是分成四个级别,分别称为L1-L4。级别越高,管理的范围就越大。L1系统一般针对阀门级,L2系统是设备级(如连铸机、轧机),L3系统是车间级,L4系统则是公司级。
从某种意义上说,这些计算机系统的作用都是促进信息感知、决策和执行的统一。符合维纳的原始思想。但是,只有L1、L2系统被称为控制计算机或自动化系统,计算机自主决策的比重比较大;而L3、L4则被称为管理计算机或信息系统,主要依靠人的决策。决策机制上发生了重要的变化,这种变化,本质上就是管控尺度变化导致的。一般来说,自动化系统适合小尺度系统。
前面提到,自动控制的运行逻辑其实是人类设定的预案。原则上讲,预案分为两种:系统正常时怎么办?系统不正常时怎么办?其中,系统正常时比较简单,系统不正常的情况就要复杂得多了。这时,制定预案的工作就麻烦得多。所以,现实中针对自动化系统的措施往往是遇到故障时切换到手动模式或者停机,由人类来处理。换句话说,自动化一般只适合系统本身稳定的对象。对于“小尺度”系统,“系统正常”是一种常态,便于制定预案,便于采用自动化技术。
但是,对于车间、工厂级的“大尺度”对象,系统复杂程度急剧上升。一个子系统的问题,就可能引发整个系统的故障。对工厂级的系统来说,某台设备故障、生产衔接不上、操作不规范、质量异常等会常态化发生。这些问题发生时,整个系统未必有预案,往往需要人来灵活处置。其中,信息系统的一个作用就是帮助人类完成这种决策的。
3 感知与认知
计算机系统管控的范围变大时,还会面临另外一个挑战,就是感知到认知的变化。大系统的管理需要较强的认知能力,而计算机的认知能力总体上要弱得多。
传感器一般只能获得基本的物理量。如温度、压力、流量、光线强度、开关状态等。这些信息中往往包含着更加深层次的信息。比如,传感器测量烟气的温度为300℃,其中包含了“烟道堵了、需要清扫”的信息;传感器测量带钢表面光线的明暗,这些信号则可能包含了“表面质量不良”的信息。从信号中获得这类深层次信息的过程,就是从“感知”到“认知”的过程。
对自动化系统来说,系统接收的信号本身具有明确的物理信息,如温度、压力、流量、开关状态。但管理一个车间、工厂时,却需要“认知”能力。比如,人们要知道设备是不是出现故障、操作是不是合规、物流是不是顺畅、质量是不是合格,这些都需要认知能力。在传统的技术水平下,“认知”主要是依靠人的能力。如果计算机没有认知能力,也就难以自动做出决策。这样,决策工作也就只能交给人类完成。事实上,信息系统的主要作用,就是帮助人们进行决策。
我们知道,工业互联网和工业大数据是智能化重要的支撑手段。这两种手段,都有助于提升计算机的认知能力。
同时,工业互联网的应用,让计算机的管控范围增大、处理问题的复杂度也增加。这时,也需要提升计算机的认知能力,才能让互联网的优势发挥出来。通过提升认知能力,计算机可以帮助人们更好地监控设备和生产状态、操作的合规性、质量和成本情况等。
4 工业互联网与人机融合
如前所述,传统的自动化系统和信息化系统是相对对立的。两类系统的决策主体不一样。计算机的认知能力相对较差,是计算机难以处理大系统问题的重要原因。所以,认知能力的提升,必然会推动智能化的发展。
在工业互联网时代,原本相对独立的自动化和信息化系统能够更为密切地融合在一起,从而实现大尺度的决策优化。工业互联网白皮书提到了三个要素:智能的机器、高级算法和工作中的人。其中,高级算法的一个重要作用就是提升机器的认知能力,从而促进决策工作的人机融合。
在工业互联网的时代,工厂乃至整个产业链的信息都可能被接入系统,系统的规模往往会大于原来企业级的信息系统。所以,传统的信息系统一般只处理非实时的任务,实时的任务只能交给控制系统来处理。但是,有些实时发生的问题,会影响到全局,这时传统的计算机系统就无法处理了,就会带来经济上的损失。
要解决这个矛盾,就需要依靠第三个要素,即“高级算法”。人类的大脑做不到每秒处理成千上万的数据,但机器能够做到。在这些数据中,正常的信息是不需要麻烦人类管理者的。机器可以帮助人类从海量实时数据中完成“从感知到认知”的任务,帮助人类发现需要处理的问题,再把信息传递给人类、让人类进行决策。这样,就形成了人机共同决策、优势互补的决策方式。
这种思路在实践中是行之有效的。例如,钢厂的煤气系统涉及到众多设备,而煤气的生产和使用必须是动态平衡的。由于煤气平衡涉及到生产的安排,很难实现完全自动化。而与煤气相关的数据又太多、变化太快,人类的决策往往会产生失误。采用上述人机融合的办法,就可以很好地解决这个问题。
5 人机融合对现代管理的意义
从管理的角度看,人机融合具有重大意义。通俗地讲,计算机可以告诉操作工人,他的操作对公司经营有什么样的影响;而管理者也可以洞悉工厂运行细节,把企业的管理提升至现代化水平。
举例来讲,钢厂的发电机组往往是用来消耗富余煤气的。但是,煤气总体上富余并不意味着每个时刻都富余。如果在煤气供给不足时多发电,对企业效益反而不利。利用互联网等智能化技术,电厂的操作工就知道,当前多发电是否对公司效益有利。从某种意义上说,这就是工人参与管理。
管理者可以更加有效地了解生产现场。大钢厂有成千上万个岗位,高管无法监管每一个岗位的工作是不是合规。但是,利用工业互联网和数字化技术,高管就有能力管理到细节。比如,某台设备异常报警几十分钟,操作工应该处置而没有反应。这时,计算机就可以把信息传给公司高层。
6 对误区的预防
目前,我国在推进智能化的过程中出现了一些误区。比如,过度迷信机器学习算法,尤其是那些复杂的算法。这与我国研究智能化的专家缺乏工厂工作经验和数据分析、建模经历有关。事实上,数字化的算法在很大程度上源于专业知识和经验,数据分析一般是对知识、经验的精细化、代码化。例如,“从感知到认知”算法,往往是通过标准化的方法来实现的,一点也不神秘。也就是说,针对特定的场景建立标准,而所谓“从感知到认知”的过程往往就是“判断是否超标”的过程,出现超标时提醒管理者和协同方。换句话说,智能化的推进也要与传统上、行之有效的管理方法结合在一起。
智能化是针对大系统的问题。这个特点还会影响到系统的建设和推进。一般来说,小系统便于顶层设计,大系统难以顶层设计。智能化系统的顶层设计难度就很大。
为此,推进智能化应该采用持续改进的逻辑。也就是说,智能化的功能是在应用过程中不断增加上去、不断修订和完善的,而不是一次到位地提出解决方案。这一点与自动化、信息化系统建设是不一样的。这个逻辑又会进一步延伸下去,会对工业互联网系统架构提出要求、会对企业的人员配置和培训提出要求。
日本人提出的工业价值链参考架构(IVRA),就体现了这种思想。按照这个架构,智能化的推进过程,就是通过PDCA对资源管理进行持续改进。PDCA是现代化企业所熟知,且行之有效的管理方法,而在数字化网络化时代,计算机可以让PDCA的能力显著增强,并落实到每一个具体的场景和时间段。
内容来源:世界金属导报

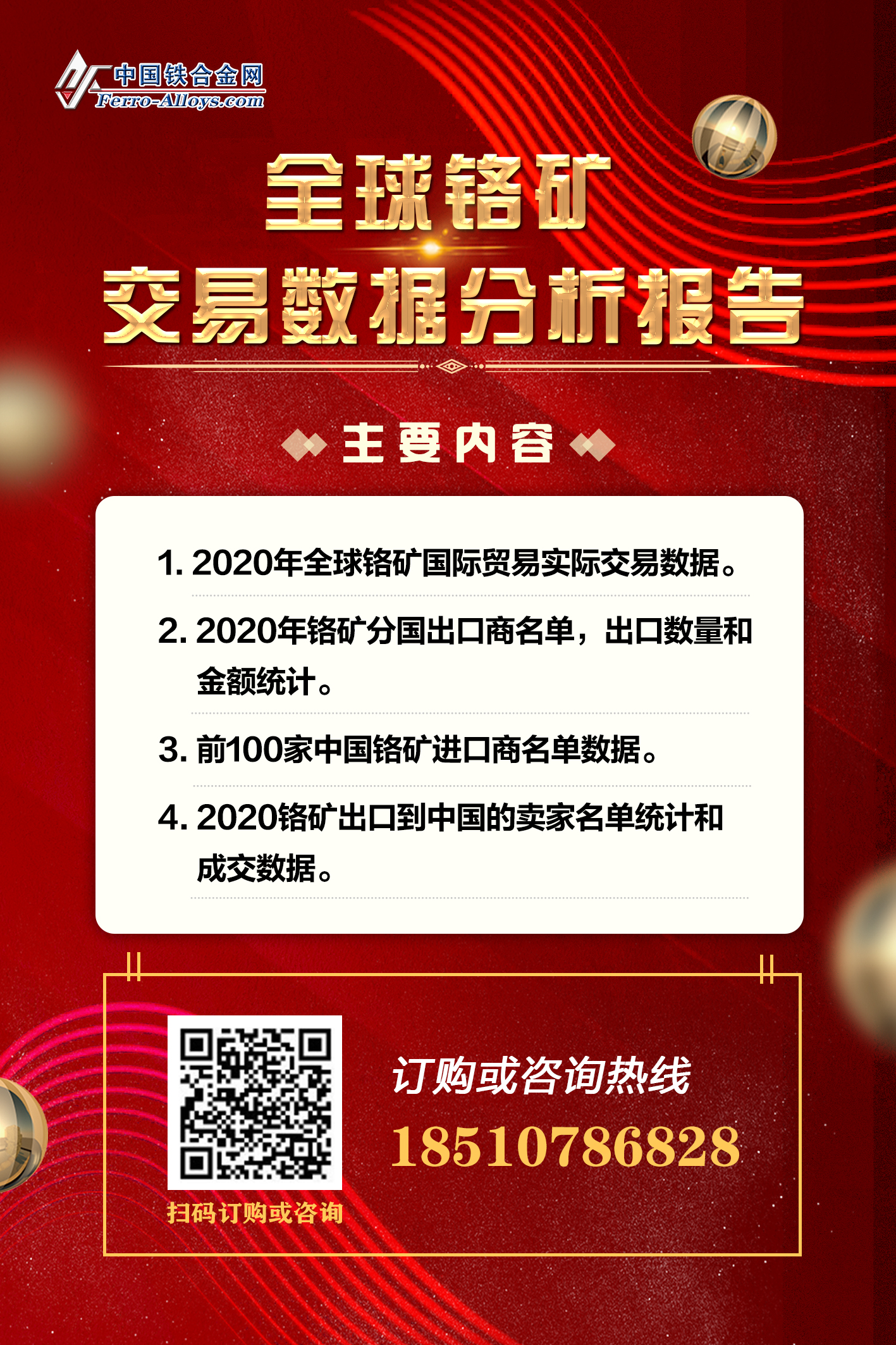
中国铁合金网版权所有,未经许可,任何单位及个人均不得擅自拷贝或转载,否则视为侵权,本网站将依法追究其法律责任,特此郑重声明!
- [责任编辑:kangmingfei]
评论内容